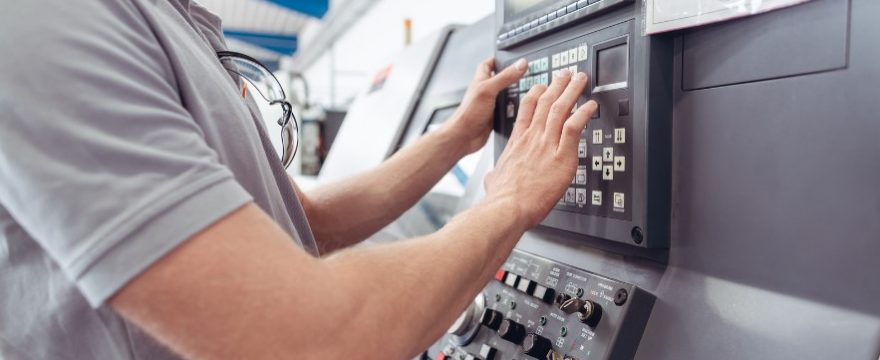
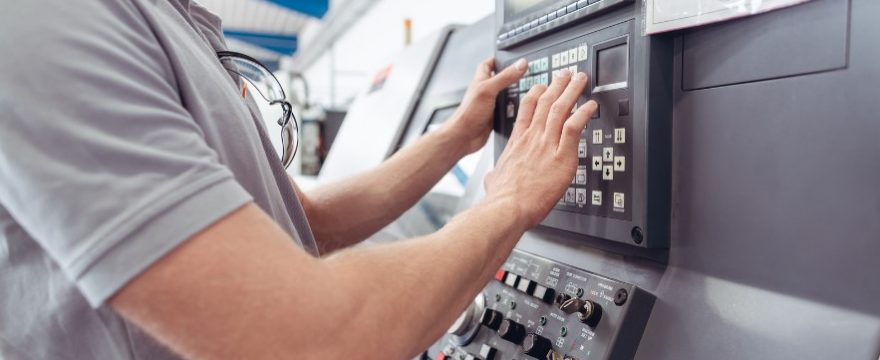
Stop losing orders. Learn how to reduce the cost per part!
Choosing a new machining center is a crucial moment for many companies in the manufacturing industry. It’s a decision that carries great responsibility, especially because it can significantly affect productivity and competitiveness. There are two main approaches to selecting a new machining center, but only one minimizes risks and ensures a grounded, safe decision-making process.
The Safest Method to Choose Your Machining Center
Selecting a machining center is a critical decision for any manufacturing company. This process not only involves significant responsibility but can also have a direct impact on the company’s productivity and competitiveness. There are two completely opposite approaches to tackling this decision: one is risky, while the other is much safer.
Let’s analyze them in detail.
The Traditional Method: Fast but Risky
The traditional method of selecting a new machining center is still very common today but hides pitfalls that are often overlooked. Typically, the process starts by attending industry trade shows, where one can quickly engage with various machine tool manufacturers. During these events, you gather information about the latest technological innovations, analyze the main features of the machines (such as speed, power, and capability), and obtain detailed quotes.
After the trade show, the next step involves one-to-one meetings with suppliers to further explore the technical specifications and capabilities of the proposed machines. At this stage, however, the most delicate phase begins: comparing the offers. This step can be extremely risky as it relies exclusively on theoretical information provided by manufacturers, without practical test.
The result?
A decision based on incomplete data, potentially leading to lacking or even wrong choices.
The Scientific Method: Four Steps for a Conscious Choice
There is a much safer alternative approach that minimizes the risks associated with choosing a machining center. This method unfolds in four steps, with the first two being theoretical and the last two practical. Here’s how it works:
1. Process Analysis
The first step begins with an in-depth analysis of your production process. This involves studying the part (or family of parts) you need to produce, hypothesizing the clamping equipment, and identifying the necessary machining operations. The goal is to identify the best solution for your specific needs.
2. Detailed Design
In the second step, process engineers thoroughly analyze technical parameters: part clamping, tools, and machining operations. This study helps precisely define cutting speeds and other critical factors, moving closer to the ideal solution.
3. Practical Test
The third step represents the first practical interaction with the machine. A demo machining center is equipped, and a real Test Drive is conducted. During this phase, the fixtures and tools defined in the previous steps are used to machine the real component, testing its feasibility.
4. Performance Check
In the final step, you verify whether the theoretical assumptions were confirmed in practice. The part is subjected to precise measurements using measurement machines, and aspects such as tolerances, surface finish, and compliance with the technical drawing are analyzed. This phase also evaluates cycle time and overall product quality.
Why Choose the Scientific Method
Unlike the first approach, the second method starts with the machining process rather than the machine itself. This allows for a precise definition of production needs, minimizing risks associated with the purchase. The machine is chosen only after verifying which solution best fits the specific needs of the company.
If you want to take this path, our team of technical tutors is ready to guide you through the four steps, helping you make an informed decision and reducing the risks associated with the selection process.
The Advantages of the Scientific Method
The scientific method provides a structured and concrete pathway to ensure the chosen machining center aligns perfectly with your needs. By focusing on machining the part and validating hypotheses through practical tests, it eliminates uncertainties associated with purely theoretical data. This approach allows you to make decisions based on tangible results, ensuring a safer and more focused investment for your company.
Rely on a Technical Tutor for Your Choice
If you want to adopt the Scientific Method to select your next machining center, contact us.
Our technical tutors will guide you through these four steps, offering personalized advice to ensure the best investment for your company.
Don’t let the risk of a wrong choice compromise your productivity. Rely on a structured method based on analysis and practical tests to make informed and secure decisions.
Phone: +39 030 800673
Email: info@portaproduction.com
To your results,
Maurizio Porta
Master Trainer PORTA PRODUCTION METHOD